Quick Facts:
- Pump and compressor stations are used to transport unrefined petroleum, petroleum products, and liquefied natural gas through pipelines.
Overview
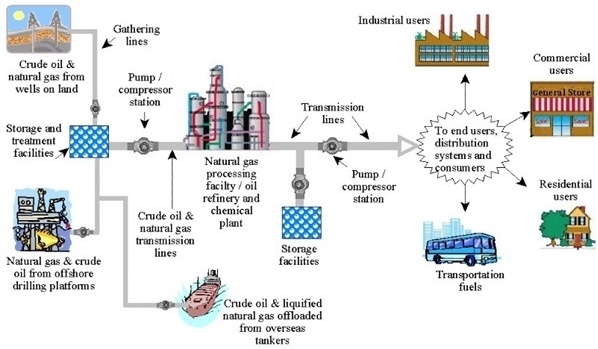
Crude oil, petroleum products, and natural gas must be transported over long distances to be made available to end-users (consumers). For purposes of transportation and storage, some natural gas is compressed into a liquid state at lowered temperature. Due to the length of pipelines and the variations in topography that they traverse, mechanical means are required to keep the commodity moving.
The commodity within the pipeline moves due to the exertion of force (pressure). As the commodity moves, the pressure is reduced, due to “friction losses” in the pipe. To keep the commodity moving, pressure must be increased along the pipeline. Pressure increases are accomplished through the use of pumps and compressors.
The operating principles of pumps and compressors are basically the same. Pumps are used on liquids and compressors are used on gas. Gases and liquids are moved through impellers in the compressor, or pump. This increases the pressure at the outlet of the component. The amount of pressure increase is dependent on design characteristics of the compressor or pump.
Pumps are positioned approximately every 20 to 100 miles, depending on the characteristics of the product and the terrain that must be traversed. In hilly terrain, pressure increases are required more frequently than on flat terrain. Likewise, compressors are normally located every 40 to 100 miles, again dependent on terrain features.
Regulation of Pumps and Compressors
Pumps and compressors in transmission lines are regulated by the Office of Pipeline Safety and state regulators under 49 CFR Parts 192 and 195.
Pumps and Compressors: Where can I learn more?
- PHMSA Community Liaison Services
- Code of Federal Regulations 49 CFR Part 192, Transportation of Natural Gas
- Code of Federal Regulations 49 CFR Part 195, Transportation of Hazardous Liquids by Pipeline
Date of Revision: 01112018